Eine zuverlässige Lösung für industrielle Schwerlastbremsen
In schweren industriellen Anwendungen wie Kranen, Bergbau und Hafenmaschinen ist die Zuverlässigkeit des Bremssystems ein kritischer Faktor für den sicheren und effizienten Betrieb von Geräten. Die hydraulische Sicherheits-Scheibenbremse der SDBH-I-Serie ist gemäß dem JB/T10917-2008 Standard "Klemm-Scheibenbremse" entworfen und hergestellt, um stabilen und sicheren Bremschutz für verschiedene kritische Industrieanlagen zu bieten. Diese Produktreihe bewältigt effektiv die strengen Herausforderungen der Bremsleistung und Zuverlässigkeit in industriellen Umgebungen durch ihre einzigartigen Designprinzipien, präzise Steuerung der Betriebsparameter und integrierte Zustandsüberwachungsfunktionen.
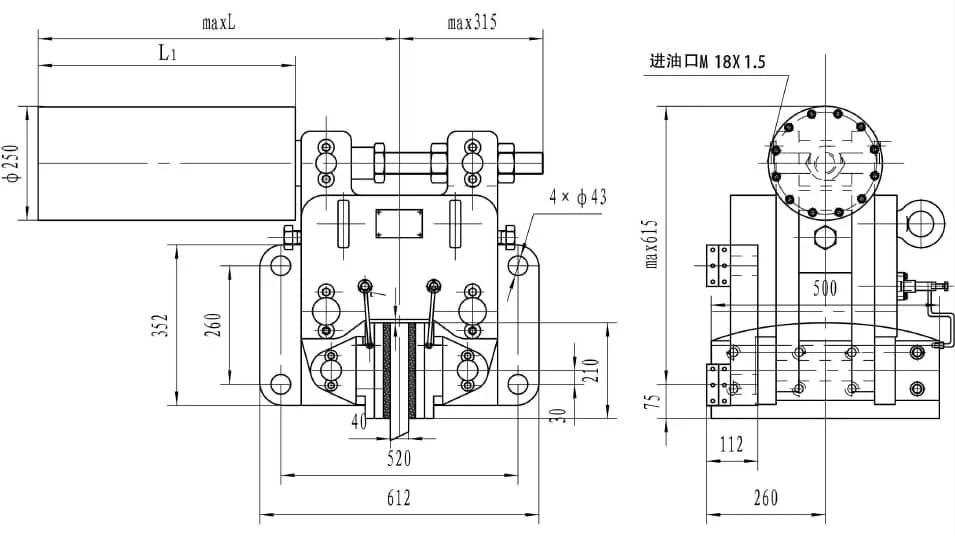
Kernmechanismus: Eingebaute Fehlerschutzfähigkeit
Die Bremsen der SDBH-I-Serie verwenden ein normalerweise geschlossenes Design mit einem hydraulischen Freigabeprinzip. Dieses Design stellt sicher, dass die Bremsen automatisch und schnell die Bremsscheibe in unerwarteten Situationen wie Stromausfall, Druckverlust im Hydrauliksystem oder Notabschaltung betätigen können. Zum Beispiel hält das System unter normalen Betriebsbedingungen die Bremse im freigegebenen Zustand mit einem Betriebsöl Druck von 8-9,5 MPa (modellabhängig, z.B. 8 MPa für SDBH250-I und SDBH365-I und 9 MPa für SDBH425-I); Sobald der Öldruck unter den festgelegten Schwellenwert fällt oder verschwindet, setzt die Bremse sofort in den betätigten Zustand zurück, was einen inhärenten Ausfallschutz bietet und effektiv Sicherheitsrisiken sowie Schäden an der Ausrüstung, die durch Bremsausfälle verursacht werden, reduziert.
Präzisionsbetrieb und hohe Anpassungsfähigkeit
- Präzise Spaltkontrolle: Optimierung der Reibungslebensdauer
- Eines der zentralen Designmerkmale dieser Bremsenserie ist ihr vollautomatisches Positionsverfolgungssystem. Dieses System stellt sicher, dass der einseitige Abstand zwischen der Reibungsplatte und der Bremsscheibe im freigegebenen Zustand präzise im Bereich von 1 mm bis 2 mm kontrolliert wird. Diese präzise Abstandskontrolle verhindert effektiv häufige Probleme wie lokale Abnutzung oder "schwebende Haftung" der Reibungsplatte bei herkömmlichen Bremsen, verlängert erheblich die Lebensdauer der Reibungsplatte, reduziert die Häufigkeit von Ersatzteilwechseln und Wartungskosten und verbessert die gesamte Betriebseffizienz.
- Flexible Installationsanpassungsfähigkeit: Anpassung an die Gegebenheiten vor Ort
- Angesichts der komplexen Installationsumgebungen in industriellen Anwendungen verfügen die Bremsen der SDBH-I-Serie über eine verstellbare Mittelhohe. Diese Funktion ermöglicht eine Feinjustierung der Bremsenhöhe während der Installation, um effektiv etwaige Installationsfehler, die vor Ort auftreten können, auszugleichen. Zum Beispiel, selbst für verschiedene Bremsmodelle unterschiedlicher Größen – wie das Modell SDBH250-I mit einer L-Dimension von 595 mm und die Modelle SDBH365-I und SDBH425-I mit einer L-Dimension von 790 mm – vereinfacht die verstellbare Funktion die Ausrichtung und Inbetriebnahme vor Ort erheblich, verbessert die Installationseffizienz und die Anpassungsfähigkeit der Geräte.
- Standardisierte hydraulische Schnittstellen und Umweltanpassungsfähigkeit:
- Alle Modelle der SDBH-I-Serie, einschließlich des SDBH250-I, SDBH365-I und SDBH425-I, zeigen eine hohe Standardisierung und Effizienz in der hydraulischen Steuerung: Sie verwenden einheitlich ein Ölvolumen von 275 ml Zylinderöffnung, was das Design und die Wartung des hydraulischen Systems vereinfacht. Darüber hinaus können alle Modelle stabil innerhalb eines Umgebungs-Temperaturbereichs von -5 °C bis 40 °C betrieben werden, was die Umgebungs-Temperaturanforderungen der meisten industriellen Anwendungen abdeckt.
Intelligente Überwachung und Wartungsunterstützung
Die Bremsen der SDBH-I-Serie sind mit einer AC/DC-Weitspannungsöffnungsfunktion ausgestattet, die einen zuverlässigen Betrieb unter verschiedenen Stromversorgungsbedingungen gewährleistet. Der Schlüssel liegt in seinem integrierten Verschleißsensor. Dieser Sensor kann den Verschleißstatus der Reibbeläge in Echtzeit überwachen und kann mit dem Steuerungssystem der Ausrüstung verbunden werden, um eine Verriegelungsschutz- und Fehlermeldungsfunktion zu erreichen. Beispielsweise kann das System, wenn der Verschleiß der Reibbeläge die Sicherheitsgrenze erreicht, proaktiv ein Warnsignal ausgeben, das das Wartungspersonal auffordert, geplante Ersatzmaßnahmen durchzuführen, um Notabschaltungen aufgrund unerwarteten Verschleißes zu vermeiden. Diese Funktion unterstützt zustandsbasierte prädiktive Wartungsstrategien, wodurch das Risiko ungeplanter Ausfallzeiten effektiv reduziert und die Gesamtverfügbarkeit sowie die Betriebssicherheit der Ausrüstung verbessert werden.
Produktreihe und Anwendungskompatibilität
Die SDBH-I-Serie bietet Modelle mit unterschiedlichen Nennklemmkräften (kN) und Bremskräften (kN), um den vielfältigen Anforderungen industrieller Anwendungen gerecht zu werden:
- SDBH250-I Modell: Nennklemmkraft von 250 kN, erzeugt eine Bremskraft von 180 kN. Das Eigengewicht beträgt 660 kg, mit einer L1-Dimension von 378 mm. Dieses Modell wird häufig in den Hebemechanismen von mittelgroßen und kleinen Kränen sowie in Bergbauwinden mit relativ moderater Leistung eingesetzt und bietet einen standardmäßigen Sicherheitsbremschutz für diese Geräte.
- SDBH365-I Modell: Die Klemmkraft wurde auf 365 kN erhöht, während die Bremskraft 262 kN erreicht. Obwohl die L-Dimension mit der des SDBH425-I bei 790 mm identisch ist, macht das schwerere Design mit 720 kg und der L1-Dimension von 570 mm es geeignet für Hebemechanismen von Hafen- und Terminalhandlingmaschinen oder mittelgroßen bis großen Hebezeugen und bietet eine verbesserte Bremsleistung.
- SDBH425-I Modell: Als das Modell mit der stärksten Bremskraft in der SDBH-I-Serie hat das SDBH425-I eine Nennklemmkraft von bis zu 425 kN und eine Bremskraft von 306 kN. Die L-Dimension beträgt ebenfalls 790 mm, aber durch interne strukturelle Verstärkungen hat sich das Gewicht des Körpers auf 730 kg erhöht. Dieses Modell ist speziell für leistungsstarke geneigte Förderbänder, große Gießkräne und andere schwere, hochinertiale Geräte konzipiert und bietet außergewöhnliche Arbeitsbrems- und Notbremsfähigkeiten.
Sicherstellung von Zuverlässigkeit und Leistung
Die hydraulischen Sicherheits-Scheibenbremsen der SDBH-I-Serie bieten eine stabile und zuverlässige Bremslösung für schwere industrielle Geräte. Sie verfügen über integrierte Sicherheitsmechanismen, präzise Steuerung der Bremsparameter, Anpassungsfähigkeit bei der Installation und intelligente Überwachungsfunktionen. Wir sind bestrebt, Produkte anzubieten, die den Branchenstandards entsprechen, mit transparenten Leistungsdaten, um unseren Kunden zu helfen, die Produktionssicherheit zu gewährleisten und die Betriebseffizienz der Geräte zu optimieren.
Für detailliertere technische Spezifikationen oder die Produktauswahl basierend auf Ihren spezifischen Betriebsbedingungen kontaktieren Sie bitte unser technisches Support-Team.